First of all, let’s look at Actuators in general. What is an Actuator? Simply stated, an actuator is a device that makes something move or operate.
Actuators make life easier for us every day, and they are the workhorses of the industry. For example, your dentist uses an actuator to move the chair up and down.
Types of actuators by their energy source
There are three typical types of actuators used in industry as defined by their energy source.
The typical actuators in the industry include:
– Electric
– Hydraulic
– Pneumatic
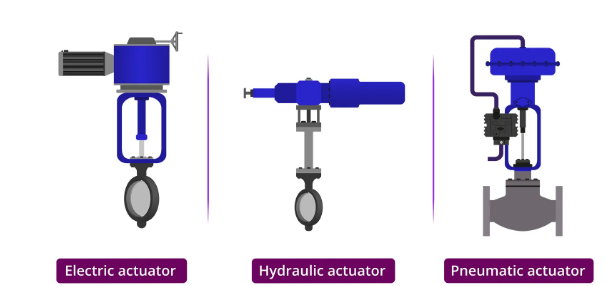
Pneumatic actuators are mechanical devices that convert compressed air energy into linear or rotary motion. Widely used in industrial automation, these actuators offer advantages such as high speed, reliability, and simplicity. This article explores the working principles, common types, and key applications of pneumatic actuators.
What is a pneumatic actuator?
By definition, a pneumatic actuator is a device that converts energy typically in the form of compressed air into mechanical motion. Within the industry, pneumatic actuators are recognised by several different names including pneumatic cylinders, air cylinders, and air actuators; all of which are one and the same.
Consisting of a piston, cylinder, and valves or ports, a pneumatic actuator can convert energy into linear or rotary mechanical motions. This is dependent on whether the application is using a pneumatic rotary actuator or a linear actuator.
Linear actuators are well suited for fitting to angle seat control valves built for high temperature and steam applications, whereas the pneumatic rotary actuators are better suited for fitting to quarter-turn valves depending on the specification of the application.
How a pneumatic actuator works?
Pneumatic actuators are reliant on the presence of some form of pressurised gas or compressed air entering a chamber where pressure is built up. Once this exceeds the required pressure levels in contrast to the atmospheric pressure outside of the chamber, it creates a controlled kinetic movement of a piston or gear which can be directed in either a straight or circular mechanical motion.
Pneumatic actuators are well suited to a wide variety of application types, serving across many different industry areas. Some of the most common applications include :
Combustible automobile engines
Air compressors
Packaging & production machinery
Railway application
Aviation.
Types of Pneumatic Actuators
-
Linear Actuators
- Single-Acting Cylinders: Use air pressure for movement in one direction and a spring for return.
- Double-Acting Cylinders: Employ air pressure for both extension and retraction strokes.
-
Rotary Actuators
- Rack-and-Pinion: Convert linear piston motion into rotary motion via a gear mechanism.
- Vane-Type: Use air pressure to rotate a vane inside a chamber, producing limited angular movement.
-
Diaphragm Actuators
- Commonly used in control valves, where a flexible diaphragm translates air pressure into linear displacement.
Key Advantages
- Fast Response: Capable of rapid cycling, making them ideal for high-speed operations.
- Durability: Minimal wear due to fewer moving parts compared to hydraulic or electric actuators.
- Safety: Non-sparking and suitable for explosive environments.
- Cost-Effective: Lower initial and maintenance costs than electric or hydraulic alternatives.
Industrial Applications
- Manufacturing: Used in assembly lines for clamping, pressing, and material handling.
- Process Control: Regulate fluid flow in chemical and petrochemical industries via control valves.
- Packaging: Drive mechanisms in filling, sealing, and labeling machines.
- Automotive: Actuate robotic arms in welding and painting systems.
If you want to learn more about low-priced products, please visit the following website: www.xm-valveactuator.com