Introduction
Pneumatic air actuators are fundamental components in automation and mechanical systems, widely used across industries for converting compressed air energy into linear or rotary motion. Their simplicity, reliability, and cost-effectiveness make them indispensable in applications ranging from manufacturing to robotics. This article explores their working principles, types, applications, and future trends.
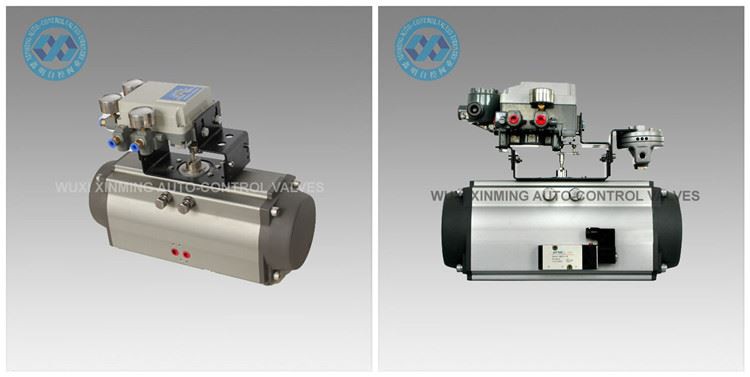
1. What is a Pneumatic Air Actuator?
A pneumatic actuator is a mechanical device that utilizes compressed air to generate force and movement. Unlike electric or hydraulic actuators, which rely on electricity or pressurized fluids, pneumatic actuators leverage the expansion of air to perform work. They are often paired with valves, cylinders, and control systems to automate processes.
2. How Do Pneumatic Actuators Work?
The operation of a pneumatic actuator is rooted in Pascal’s Law, which states that pressure applied to a confined fluid (or gas) is transmitted equally in all directions. Here’s a simplified breakdown:
- Compressed Air Supply: Air is pressurized (typically 60–120 psi) using a compressor.
- Directional Control Valve: This valve regulates airflow into the actuator.
- Cylinder and Piston: Compressed air enters the actuator chamber, forcing a piston to move linearly or rotate.
- Motion Conversion: The piston’s movement is transferred to a rod, lever, or gear to perform tasks like pushing, pulling, or rotating.
Key components include:
- Cylinder: Houses the piston and converts air pressure into motion.
- Piston Rod: Transmits force to the external load.
- Seals: Prevent air leakage and ensure efficiency.
3. Types of Pneumatic Actuators
Pneumatic actuators are categorized by their motion type:
A. Linear Actuators
- Single-Acting Cylinders: Use air pressure to move in one direction, with a spring returning the piston. Ideal for simple tasks like clamping.
- Double-Acting Cylinders: Air pressure moves the piston in both directions, offering greater control for tasks like lifting or pressing.
B. Rotary Actuators
- Rack-and-Pinion: Converts linear motion to rotary motion using a gear mechanism.
- Vane-Type: Uses air pressure to rotate a vane inside a chamber, generating torque.
C. Specialty Actuators
- Diaphragm Actuators: Employ a flexible diaphragm to isolate moving parts, ideal for sensitive environments (e.g., medical devices).
- Rodless Cylinders: Eliminate the piston rod for compact designs in confined spaces.
4. Applications of Pneumatic Air Actuators
Due to their rapid response and durability, pneumatic actuators are used in:
- Manufacturing: Assembly lines for gripping, sorting, and packaging.
- Automotive: Brake systems, engine controls, and robotic welding.
- Aerospace: Landing gear and cargo door mechanisms.
- Healthcare: Ventilators and surgical tools requiring precise motion.
- Food Processing: Hygienic, corrosion-resistant actuators for handling perishables.
5. Advantages and Limitations
Pros:
- High Force-to-Size Ratio: Capable of generating significant force even in small packages.
- Fast Response: Air compressibility allows quick acceleration and deceleration.
- Safety: No fire or explosion risk, unlike hydraulic systems.
- Low Maintenance: Fewer moving parts compared to electric actuators.
Cons:
- Energy Efficiency: Compressing air consumes energy, leading to higher operational costs over time.
- Noise: Air exhaust can be loud, requiring mufflers.
- Precision: Less accurate than electric actuators for tasks requiring micro-adjustments.
6. Future Trends
Advancements in pneumatics aim to address current limitations:
- Smart Actuators: Integration with IoT sensors for real-time monitoring and predictive maintenance.
- Energy Recovery Systems: Capturing and reusing exhaust air to improve efficiency.
- Hybrid Systems: Combining pneumatic and electric actuators for precision and power.
- Lightweight Materials: Carbon fiber and polymers to reduce weight and corrosion.
Conclusion
Pneumatic air actuators remain a cornerstone of industrial automation, balancing performance, safety, and affordability. As technology evolves, innovations in efficiency and connectivity will expand their role in smart factories, renewable energy systems, and beyond. Whether in a massive assembly plant or a delicate surgical robot, these devices exemplify the power of harnessing air to drive progress.
If you want to learn more about low-priced products, please visit the following website: www.xm-valveactuator.com