Introduction
Pneumatic actuator valves are essential components in industrial automation, widely used for controlling the flow of liquids, gases, and slurries in pipelines. These valves rely on compressed air to operate, making them efficient, reliable, and suitable for hazardous environments where electrical actuators might pose safety risks.
This article explores the working principles, types, applications, advantages, and selection criteria of pneumatic actuator valves.
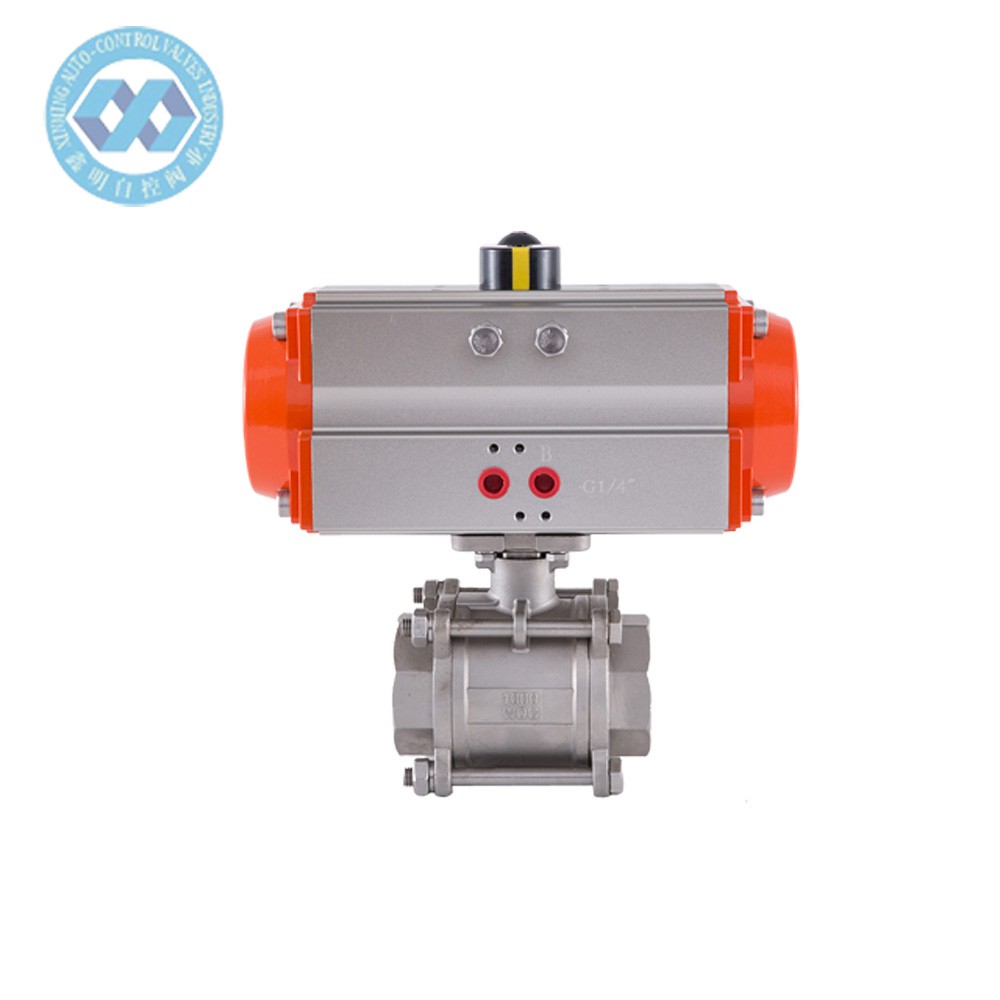
1. How Pneumatic Actuator Valves Work
A pneumatic actuator valve consists of two main parts:
- Valve Body: Controls the flow (e.g., ball, butterfly, gate, or globe valve).
- Pneumatic Actuator: Converts compressed air energy into mechanical motion to open or close the valve.
Key Components:
- Piston or Diaphragm: Moves when air pressure is applied.
- Spring (in some models): Returns the actuator to its default position when air pressure is removed.
- Positioner: Ensures precise valve positioning (optional for advanced control).
Operation:
- Air Supply: Compressed air enters the actuator chamber.
- Actuation: The air pressure pushes the piston/diaphragm, moving the valve stem.
- Valve Movement: The valve opens or closes based on the actuator's motion.
- Return Mechanism: In single-acting actuators, a spring returns the valve to its original position. Double-acting actuators use air pressure for both opening and closing.
2. Types of Pneumatic Actuator Valves
A. Based on Actuator Design
-
Single-Acting (Spring-Return) Actuators
- Use air pressure to move in one direction and a spring to return.
- Applications: Fail-safe systems (e.g., emergency shut-off valves).
-
Double-Acting Actuators
- Use air pressure for both opening and closing.
- Advantages: Higher force, no spring wear.
- Applications: Continuous process control.
B. Based on Valve Type
-
Pneumatic Ball Valves
- Quarter-turn operation, excellent for on/off control.
- Applications: Oil & gas, water treatment.
-
Pneumatic Butterfly Valves
- Lightweight, cost-effective for large pipelines.
- Applications: HVAC, food processing.
-
Pneumatic Globe Valves
- Precise flow control with linear motion.
- Applications: Chemical processing, steam systems.
-
Pneumatic Diaphragm Valves
- Ideal for corrosive or viscous fluids.
- Applications: Pharmaceuticals, wastewater.
3. Advantages of Pneumatic Actuator Valves
✅ Fast Response: Quick opening/closing compared to electric actuators.
✅ Explosion-Proof: Safe in flammable environments (no sparks).
✅ High Force-to-Size Ratio: Compact yet powerful.
✅ Low Maintenance: Fewer moving parts than electric actuators.
✅ Cost-Effective: Lower initial and operational costs.
4. Common Applications
- Oil & Gas: Pipeline control, emergency shut-off.
- Water Treatment: Flow regulation in treatment plants.
- Food & Beverage: Hygienic process control.
- Pharmaceuticals: Sterile fluid handling.
- Manufacturing: Automated production lines.
Conclusion
Pneumatic actuator valves are vital for industrial automation, offering speed, reliability, and safety in fluid control systems. Understanding their types, working principles, and selection criteria ensures optimal performance in various applications.
If you want to learn more about low-priced products, please visit the following website: www.xm-valveactuator.com